金属粉末床熔化过程有何奥秘?激光束透露,热成像的高速冷却速率
前言
使用激光束进行金属粉末床熔化是一种能够制造几何形状复杂零件的工艺,在此过程中,激光束局部熔化金属粉末以构建所需的几何形状。
这些速率在加工过程中根据零件的几何特征而变化,导致不均匀的微观结构以及各向异性的机械性能。未知的零件特性阻止该工艺用于安全关键型应用。热成像原位过程监测提供有关热场的信息,能够预测最终的材料特性。
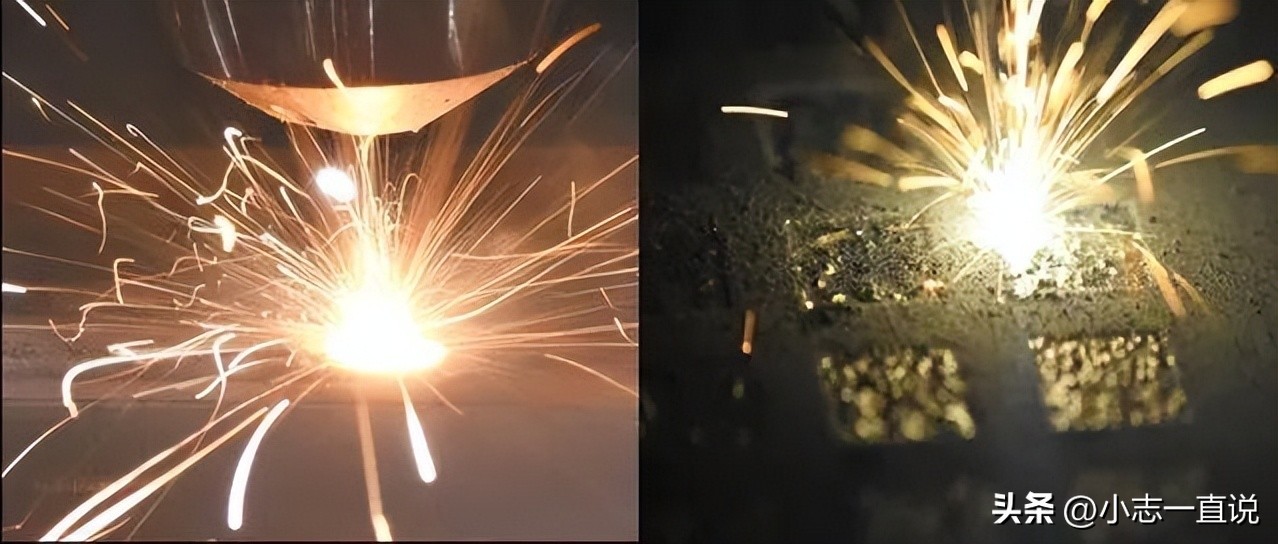
使用高速热成像相机对使用激光束进行金属粉末床熔化过程中冷却速率进行热成像测量,测量316L塔状样品制造过程中发生的冷却速率。
由于零件中的热量积聚,冷却速率随着构建高度的增加而降低,垂直和平行于构建方向测试零件的显微硬度分布,沿着构建高度观察到硬度值显著下降。
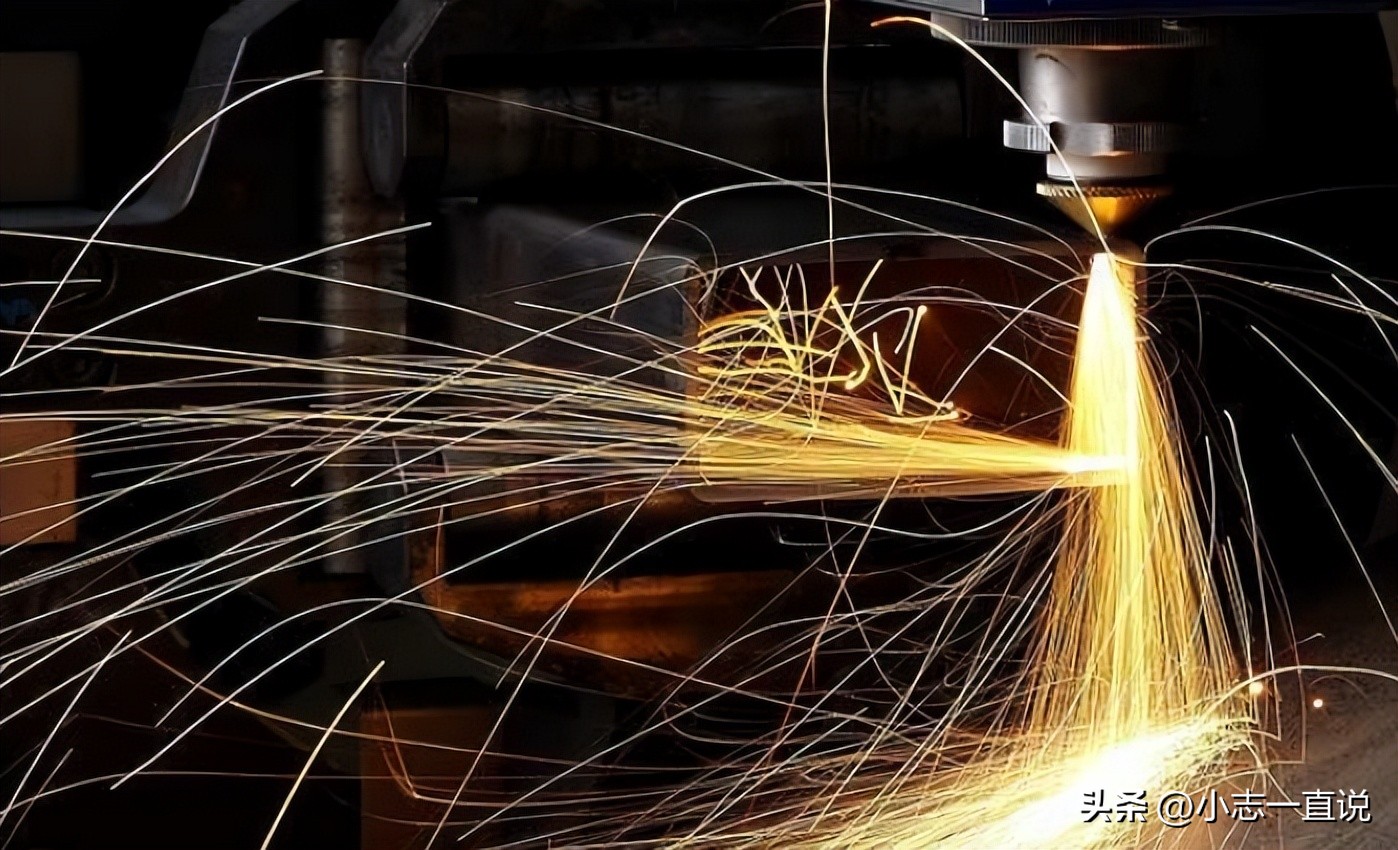
金属粉末床熔化
使用激光束进行金属粉末床熔化是一种增材制造工艺,其中激光选择性地熔化金属粉末。使用激光束进行金属粉末床熔化工艺提供了高度的设计自由度,能够制造轻质部件。
在安全至关重要的情况下,了解零件的机械性能至关重要,因为它们取决于高度动态的过程的热历史。在使用激光束进行金属粉末床熔化工艺中,熔体以高冷却速率凝固,形成具有细孔微观结构的不锈钢。
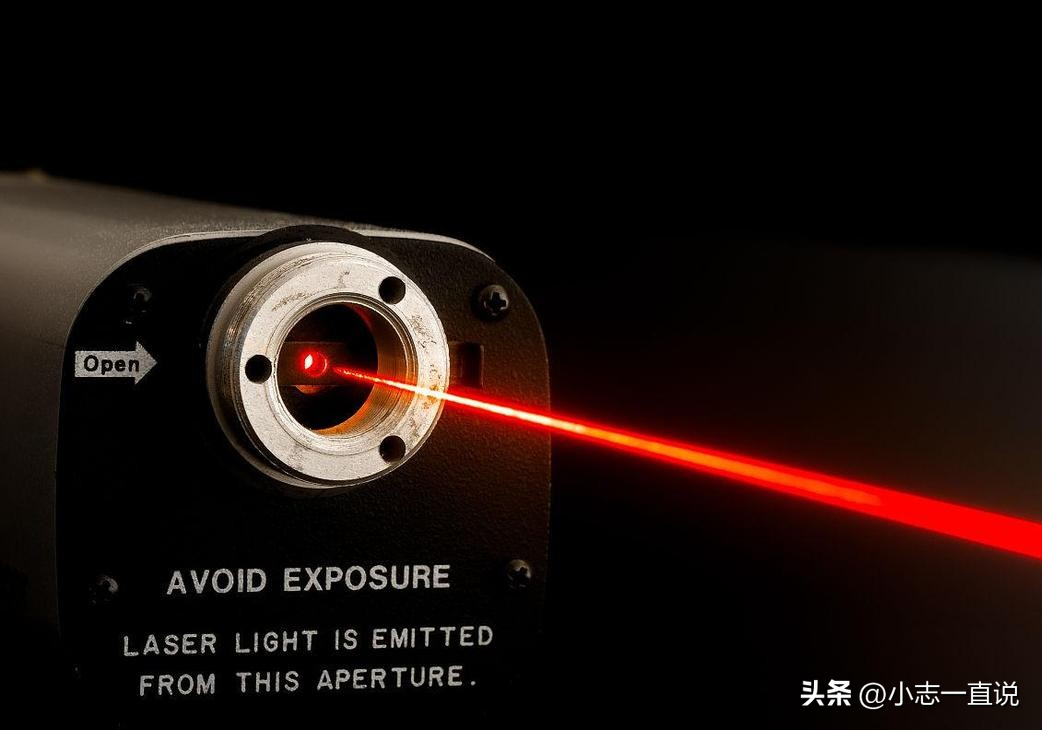
与传统材料相比,精细的亚晶结构提高了增材制造材料的强度,改变冷却速率可能会导致不同几何形状部件的微观结构和机械性能发生变化。
具有大视场的设置无法解析小型金属粉末床熔化熔池,熔池的尺寸约为几百微米。测量多个像素无法解析的小区域的温度会导致高度不确定性。
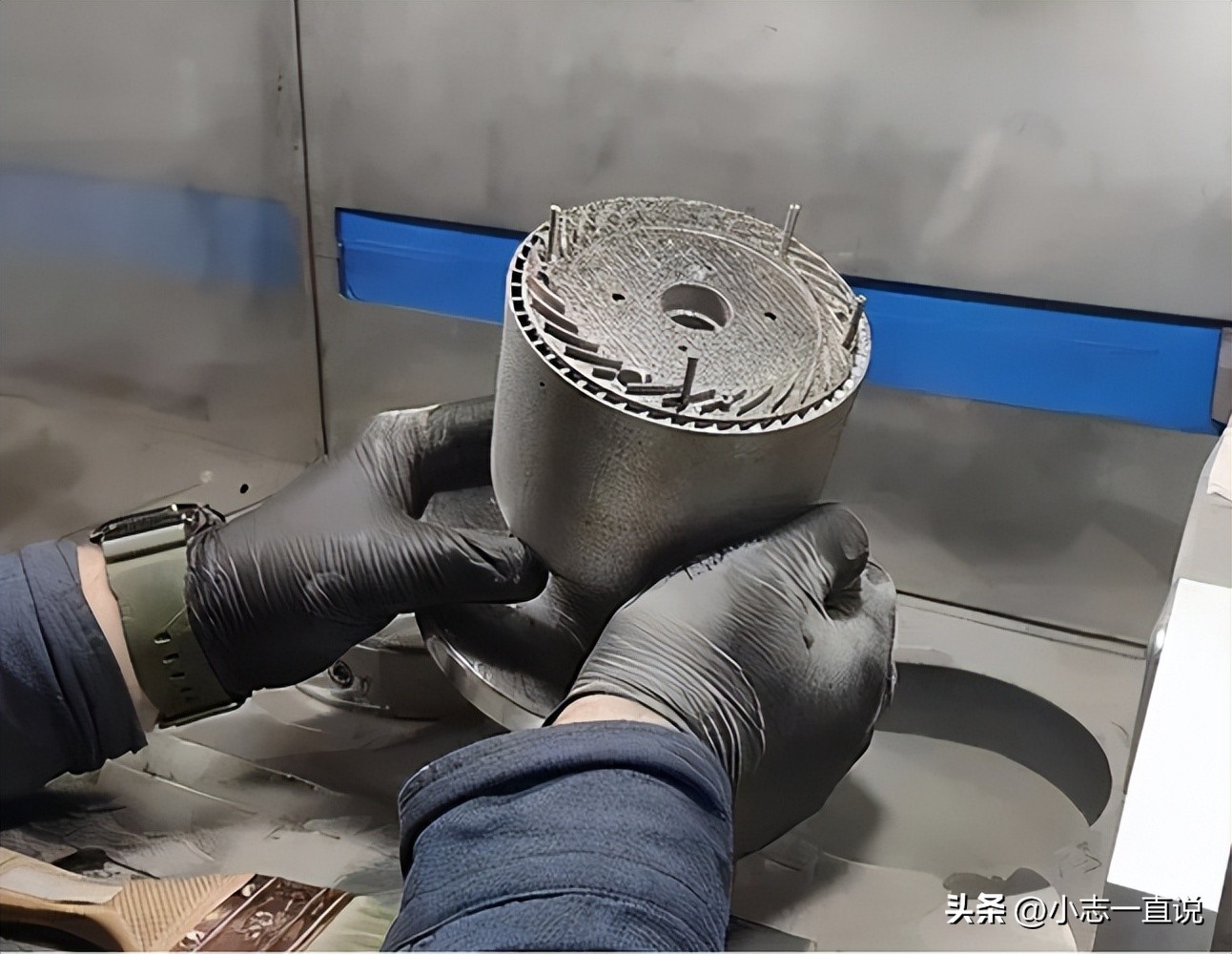
从校正数据中提取每个像素凝固后的冷却循环。通过将提取的数据拟合到简化的分析温度模型来获得冷却曲线,根据拟合冷却曲线的一阶导数计算凝固冷却速率。
冷却速率
冷却速率测量过程的第一步是检测凝固点。使用激光束进行金属粉末床熔化过程中的冷却曲线几乎呈指数级数增长。冷却速率对其计算时的温度值非常敏感。
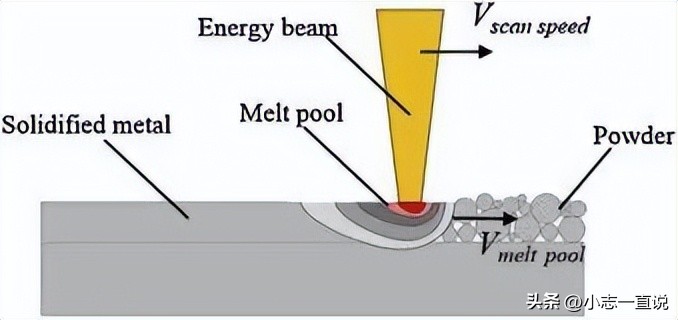
为了准确计算凝固冷却速率,必须确定凝固温度信号值。由于熔化潜热,冷却曲线在液体到固体的转变处显示出不连续性。这种不连续性的特点是冷却曲线的二阶导数的第一个最小值。
不连续处的相机值对应于凝固温度。要识别像素的相机信号中的不连续性,它必须直接位于激光路径中。只有有限数量的像素可用于识别凝固不连续性,应用多阶段程序来解决由于实验设置而导致的测量不确定性。
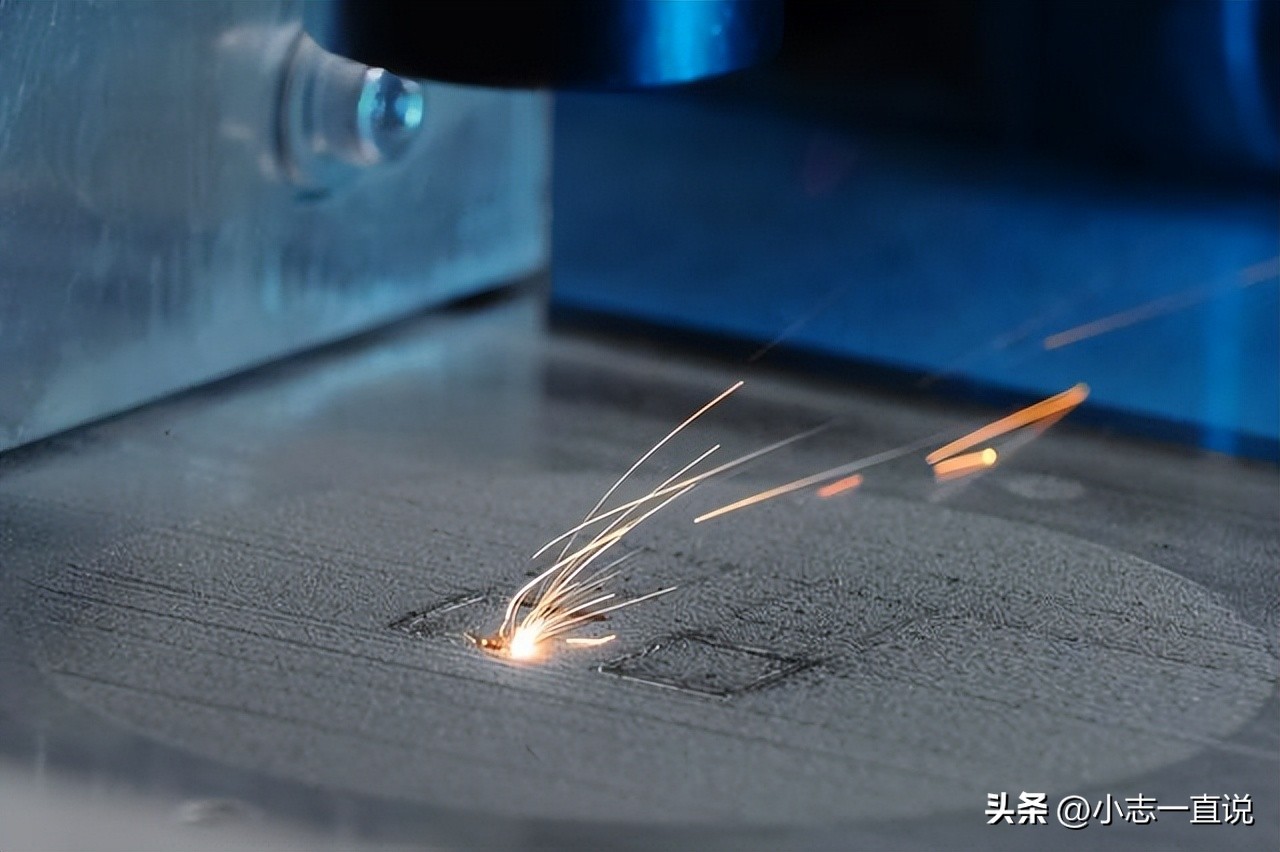
直接经过激光的像素具有该层中所有像素的最高测量值,仅使用值接近热成像相机最大值的像素来检测凝固点。可接受的范围取决于热成像设置并根据经验确定。
热成像相机的数字动态范围为16384个计数,阈值设置很重要。通过二阶中心差分算法近似这些像素的冷却曲线的二阶导数。确定二阶导数的第一个最小值以确定凝固转变的时间。如果没有检测到明确的最小值,则丢弃这些值。
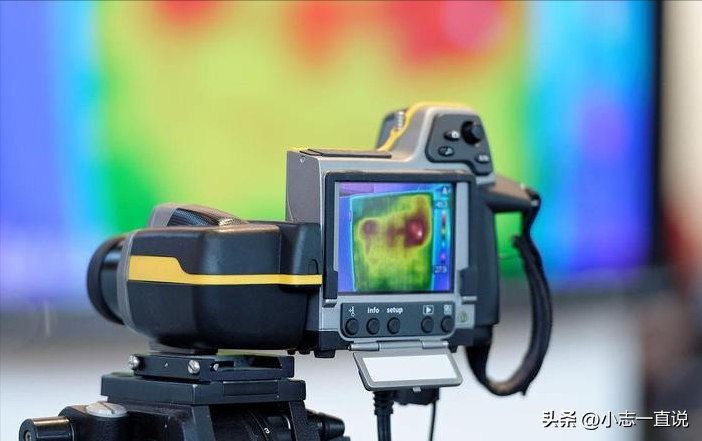
由于热成像设置的测量不确定性,预计计算出的凝固点呈正态分布。采用各层的中值作为凝固温度,由于零件制造过程中热量积聚,像素周围的温度会升高,会在热成像信号中产生偏移。
热成像相机根据零件表面的温度测量其发出的红外辐射强度。在相同温度下,真实物体发出的辐射比黑体少。两种辐射之间的比率由发射率描述,它取决于目标物体的材料、表面条件和温度。
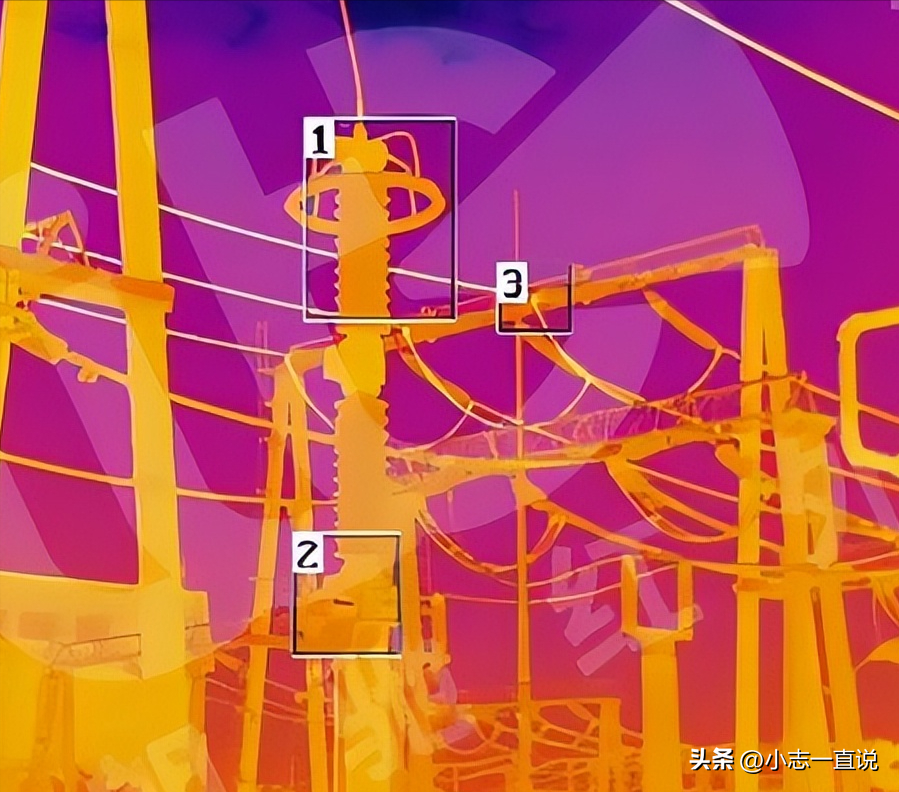
发射率还取决于波长并受视角影响,由于测量路径中的光学元件造成的损耗进一步降低了信号电平,它低于材料的实际发射率。
表观发射率是针对单个温度值确定的,假设在测量的温度范围内是恒定的,偏离该假设可能会影响测量的冷却曲线的进展。由于冷却速率是在检测到的凝固温度下确定的,该误差被认为很小时间。
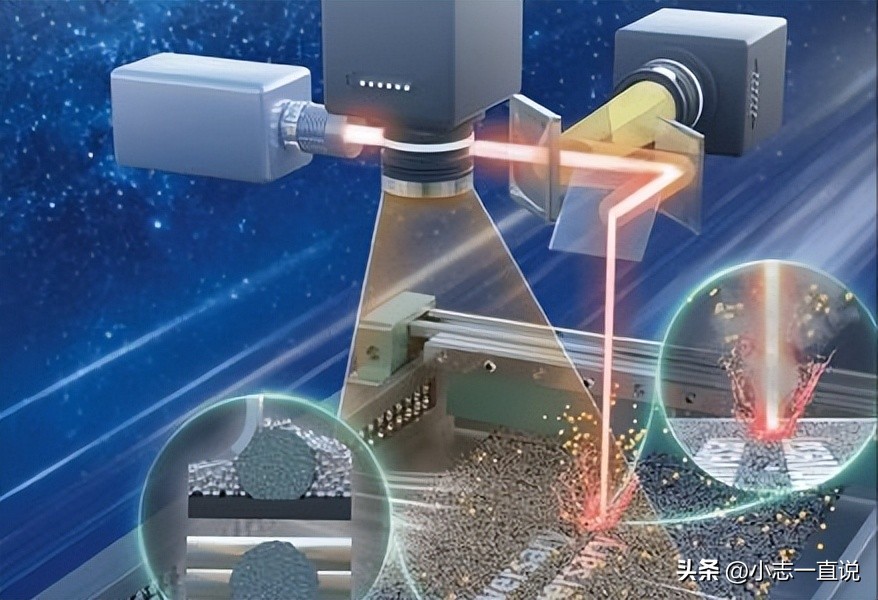
在使用激光束进行金属粉末床熔化工艺中,材料经历多次加热和冷却循环。在单个层中,这些热循环是由激光的孵化引起的。计算最后一个加热和冷却循环的冷却速率,其中超过了凝固时间。
由于渗透深度通常包括多个层,材料也会在构建方向上重新熔化,这会在测量的冷却速率和凝固的微观结构之间产生偏移。使用激光束进行金属粉末床熔化工艺中的层厚度在几十微米范围内。
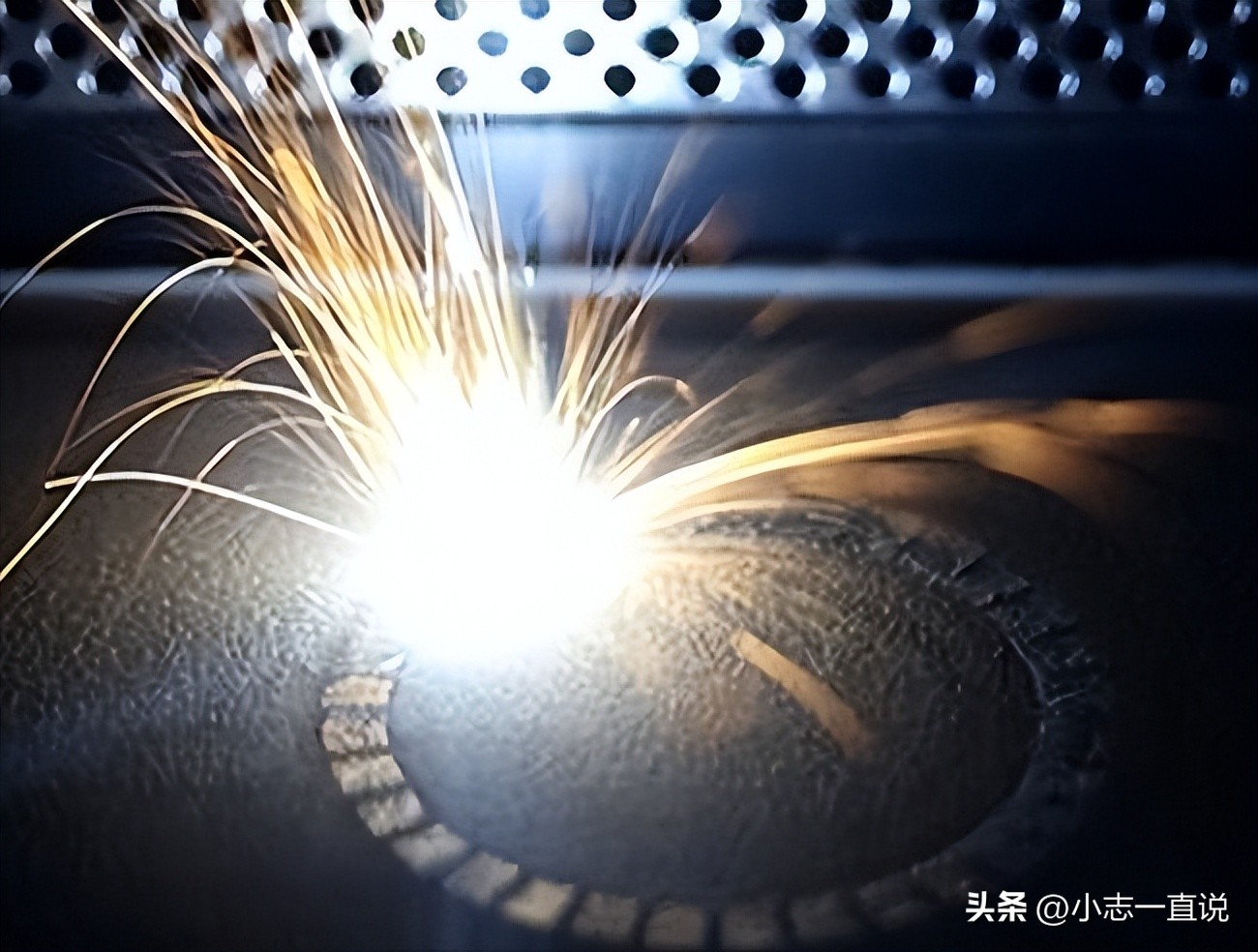
冷却曲线的拟合
为了计算冷却速率,使用提出的使用激光束进行金属粉末床熔化过程的分析温度模型对提取的热成像数据进行拟合。与测量数据的分段插值相反,分析模型的拟合包括冷却曲线的所有数据点。它对于由于测量误差而导致的信号偏差更加稳健。
拟合模型提供了一条连续的、物理上可解释的曲线,用于评估冷却速率。凝固后的温度近似于半无限棒,其最顶层和较高温度时间。假设热量仅通过传导传递,忽略与温度相关的材料特性和相变,热量均匀地注入棒材顶层的体积分数中。
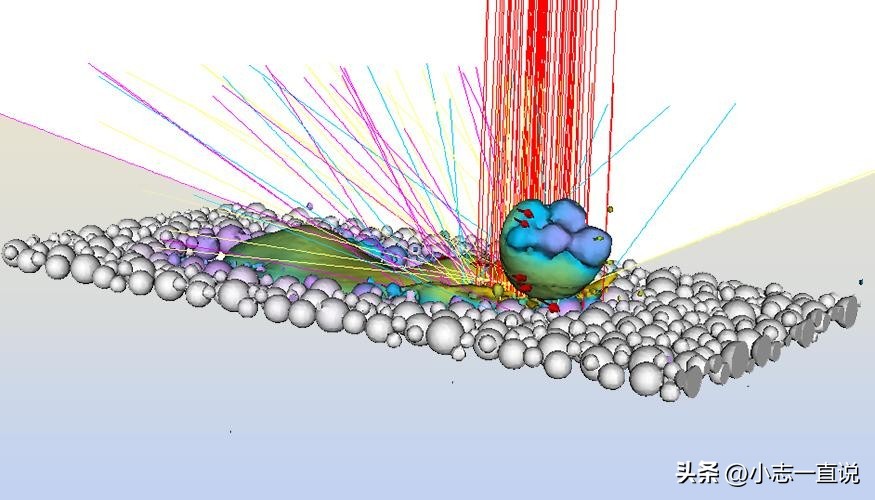
机器配备400W光纤激光器,光束直径为100 m。使用热像仪测量金属粉末床熔化过程中的热场,相机灵敏度覆盖的光谱范围为2m至5m。
50毫米镜头配有透光率为10%的内部中性密度滤光片,目的是减少入射辐射并防止相机传感器在测量较高温度范围时饱和。
进入腔室的光学通道是通过锗长通滤光片窗口。滤光片的直径为50毫米,在相机光谱范围内的透射率>85%。该设置覆盖的视野为最高分辨率。由于大气衰减和观察窗的通光孔径,朝向视场外边界的撞击辐射衰减不断增加。
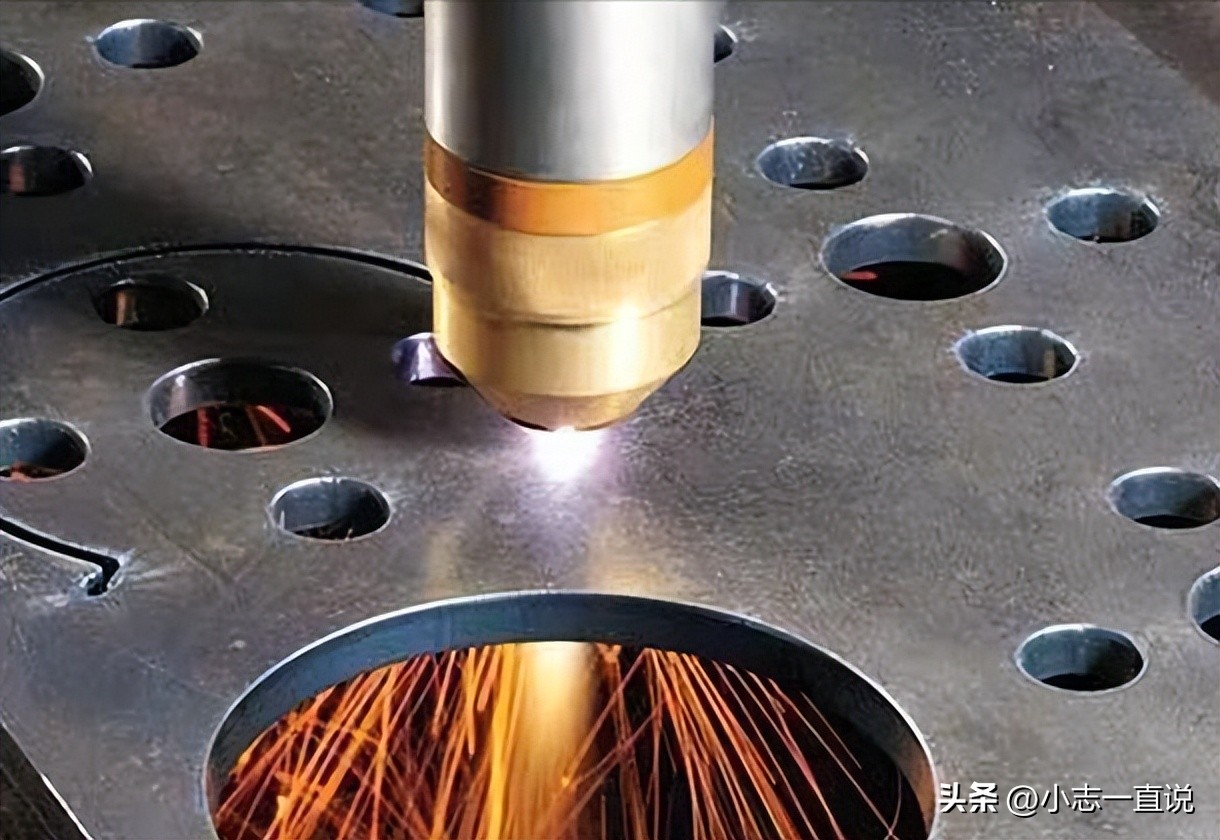
使用190W的激光功率和800mm/s的扫描速度对轮廓进行单次后曝光。扫描矢量平行于样本边缘,导致扫描矢量长度恒定为10毫米。零件和扫描图案绕Z轴旋转30°,以防止暴露在保护气流中。
在随后的建造工作中制造了第二套双塔,以调查建造工作之间的任何潜在差异。制造完成后,使用带锯将塔从构建板上切割下来。对于构建高度的前15毫米,每1毫米测量一次冷却速率。
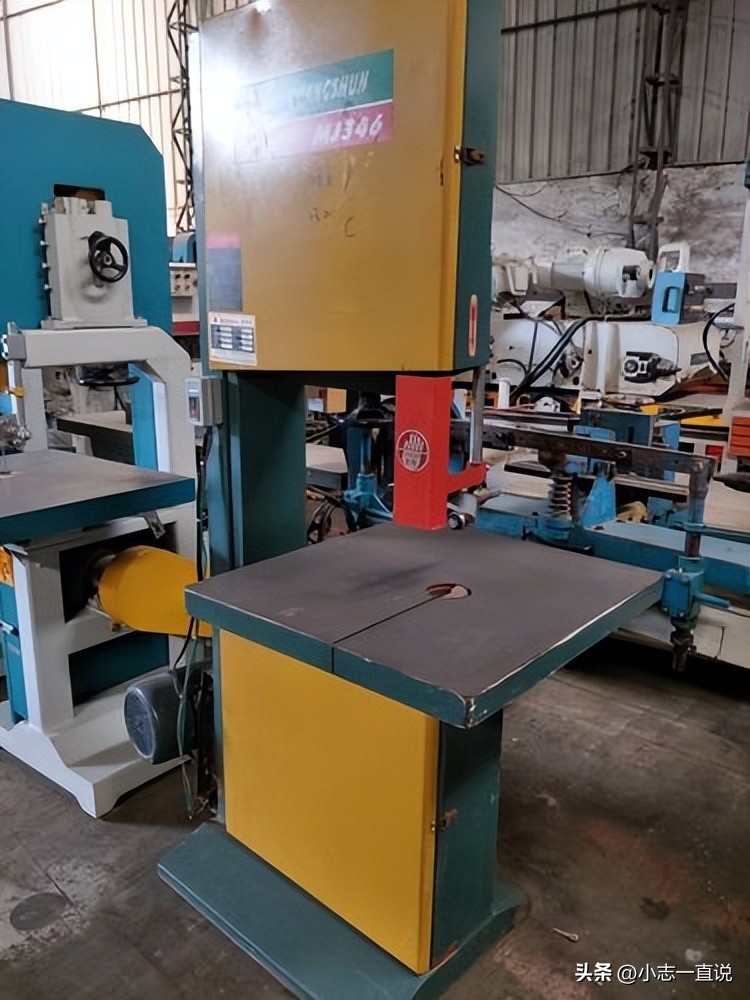
对每个建造作业的两座塔,使用磨料切割机对样本进行切片,每个构建工作中的一座塔沿着XZ平面中心切割,每一半被分成高度为25毫米的部分。每个构建作业的第二个塔沿着XY平面每隔10毫米进行剖切,然后将横截面嵌入、研磨和抛光。
晶间单元结构是使用激光束进行金属粉末床熔化制造的316L的主要强化机制。该过程中的冷却速率会影响该亚晶粒结构的晶胞尺寸。随着晶粒细化,晶粒之间的位错运动需要更高的应力。
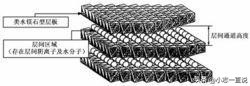
单晶位错所需的最大屈服应力是晶粒尺寸,通过将应力替换为硬度,将晶粒尺寸替换为晶胞尺寸,使用激光束进行金属粉末床熔化制造的316L的显微硬度与晶胞尺寸具有良好的相关性。
所有监测层在凝固温度下的相机强度值,每个单层中的像素值均呈正态分布。尽管凝固转变的温度是特定于材料的常数,但强度的平均值逐渐增加。这种偏移是由于零件中的热量积聚导致表面温度升高而引起的。
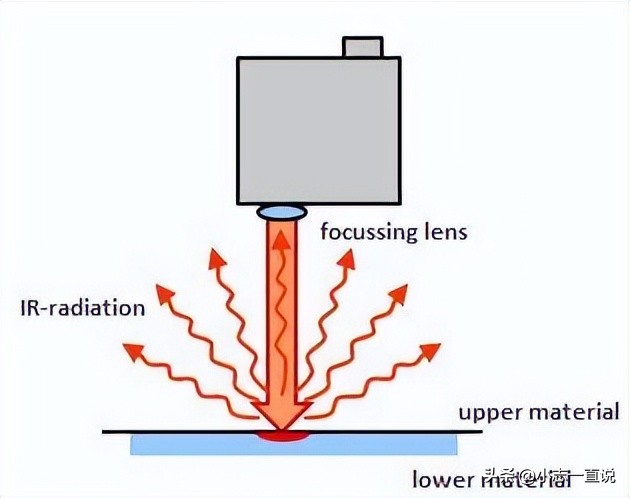
像素的相机值受到周围环境温度的影响,零件的表面温度对熔池像素的信号值有贡献,更高的热成像分辨率将减少这种偏移,通过评估与每层凝固温度相对应的相机值来补偿该影响。
冷却速度
塔的冷却速率曲线显示出相似的级数,各种平均值的最大相对标准误差为1.58%。冷却速率测量方法具有高再现性,对于构建平台上不同位置的相同几何形状以及各个构建作业,制造过程中的冷却速率是可重复的。
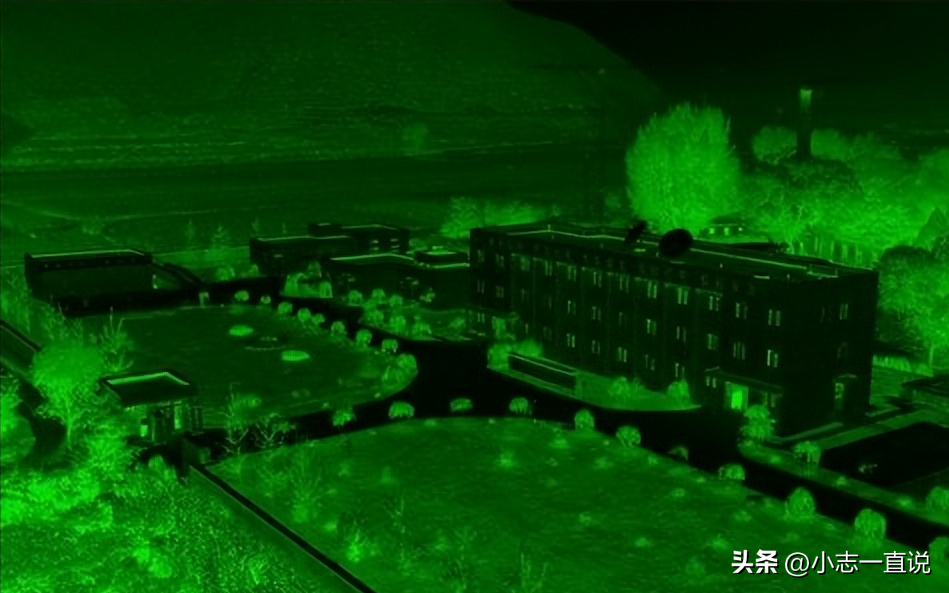
每层冷却速率的偏差包括测量不确定性、数据处理误差和冷却速率的实际变化。单层内的冷却速率发生变化,导致标准偏差约为20-30%,小标准误差表明单层内的偏差主要归因于扫描模式。激光转折点的冷却速率较低,因为激光在同一区域停留的时间较长。
冷却速率随高度的降低是由于塔内热量积聚造成的。零件中温度的升高会导致熔池和零件最顶层之间的温度梯度降低,热量积累的水平取决于ILT,缩短ILT会增加表面温度。如果层之间有足够的冷却时间,则可以避免热量积聚。
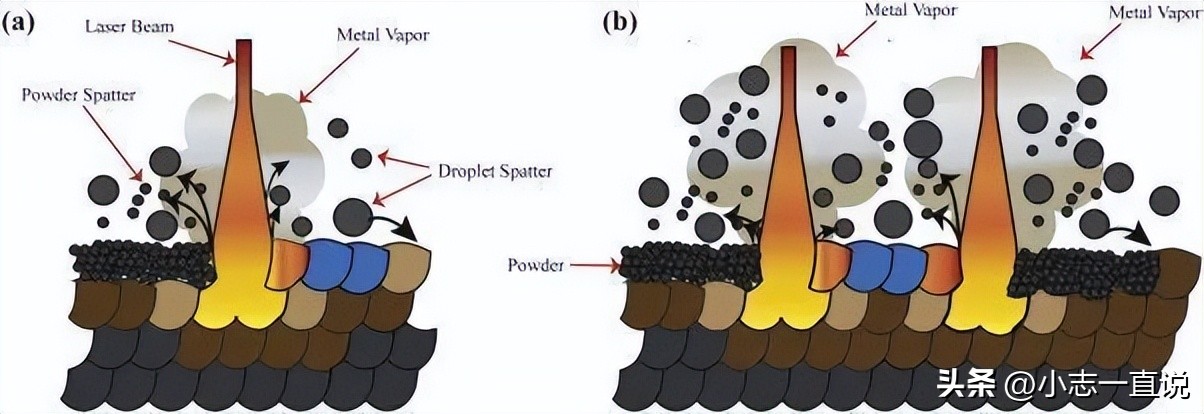
随着高度的增加,零件平面的硬度显著降低,两个塔的XY平面的硬度分布在两个样品之间没有显著差异,两个构建作业之间相似零件的局部机械性能的可重复性,平面上的硬度分布也呈现下降趋势。
XZ平面内的硬度值略高于XY平面内的硬度值,具有各向异性,归因于各个层的多次重熔。
通常可以通过冷却速率测量方法来识别微观结构和机械性能的局部变化,但机械性能的预测是不可能的,因为相关性基于为每层确定的平均值。
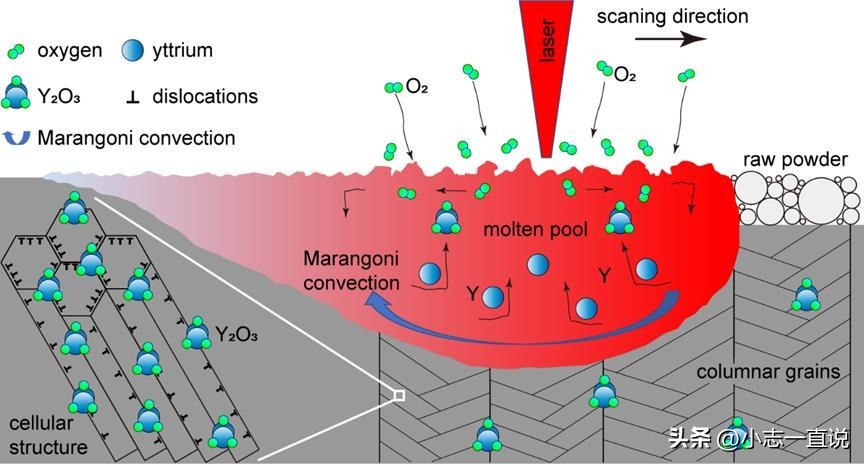
结论
测量使用激光束进行金属粉末床熔化过程中冷却速率的方法沿着构建高度在多个层中测量冷却速率。沿着构建高度、垂直和平行于构建方向测试HV1显微硬度分布,将零件的冷却速率和机械性能关联起来。
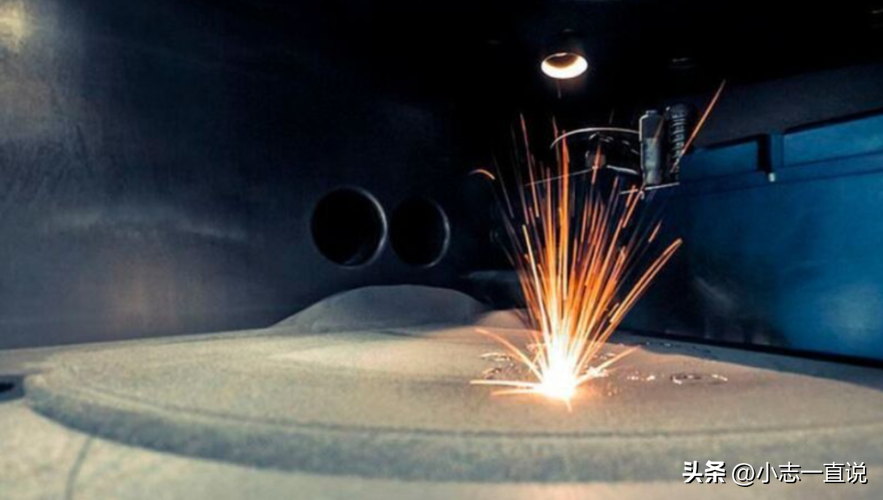